Laser Marking System for Medical Industry
In recent years, advancements in new applications in medical device manufacturing has enabled the industry to produce smaller and lighter medical devices and implants. These smaller devices have presented new challenges in traditional manufacturing and laser systems in medical device manufacturing technology has gained popularity due to its precise material processing methods.
Medical device manufacturers have a unique set of requirements for high precision markings on their medical devices. They are looking for permanent, legible and accurate markings that are defined by government guidelines for Unique Device Identification (UDI) on all medical devices, implants, tools and instruments. Medical device laser marking helps meet strict product identification and traceability guidelines for direct part marking and has become a common process in medical device manufacturing. Laser marking is a non-contact form of engraving and offers consistent high quality laser marks at high processing speeds while eliminating any potential damage or stress to the parts being marked.
Laser marking is the preferred method for product identification marks on medical devices such as orthopedic implants, medical supplies and other medical instruments because the marks are corrosion resistant and withstand sterilization processes such as, passivation, centrifuging, and autoclaving.
The most popular metal used by manufacturers in the making of medical/surgical instruments is stainless steel, nicknamed surgical stainless steel. Most of these instruments are small in size, making the production of clear and legible identification marks that much more challenging. Laser markings are resistant to acids, cleaners or bodily fluids. As the surface structure remains unchanged, depending on the labeling process, surgical instruments can be kept clean and sterile easily. Even if implants remain inside the body for a long time, no materials from the label can detach themselves and harm the patient.
The marking contents remain legible (also electronically) even under heavy use and after hundreds of cleaning procedures. This means that the parts can be clearly tracked and identified.
Advantages of the laser technology in medical industry:
Marking content: Traceability codes with variable contents
* A wide range of different markings can be created from variable content without retooling or tool changes
* Marking requirements in medical technology can be implemented easily thanks to flexible and intelligent software solutions.
Permanent labeling for traceability and quality assurance
* In medical technology, instruments are cleaned very often with harsh chemicals. These high requirements can often only be implemented with laser markings.
* Laser markings are permanent and are abrasion, heat and acid resistant.
Highest marking quality and accuracy
* It is possible to create tiny details and fonts that are highly legible
* Precise and small shapes can be marked with acute accuracy
* Marking processes can be combined to clean the material after processing or to provide a higher contrast (e.g. Data Matrix codes)
Flexibility with materials
* A wide range of materials including titanium, stainless steel, high alloy steels, ceramics, plastics, and PEEK - can be marked with the laser
Marking takes seconds and allows greater output
* High speed marking is possible with variable data (e.g. serial numbers, codes)
* A wide range of markings can be created without retooling or tool changes
Non-contact and reliable material processing capabilities
* There is no need to firmly clamp down or fixate materials
* Time savings and consistently good results
Cost-efficient production
* No set-up time with the laser, regardless of large or small quantities
* No tool wear
Integration into production lines is possible
* Hardware and software-sided integration into existing production lines is possible
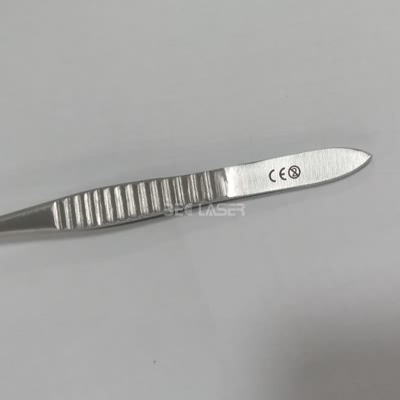
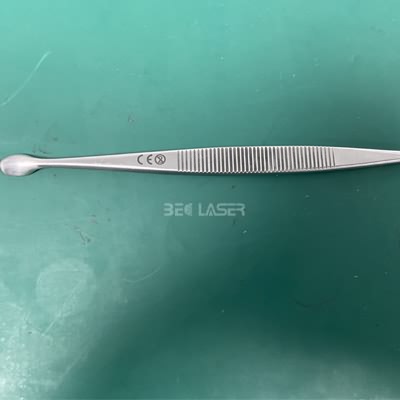
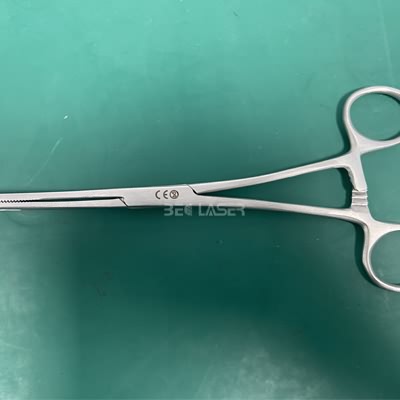
Laser Welding System for Medical Industry
The addition of laser welding machine technology to medical industry has greatly promoted the development of medical devices, such as the housing of active implantable medical devices, radiopaque markers of cardiac stents, earwax protectors and balloon catheters, etc. They are all inseparable from the use of laser welding. The welding of medical instruments requires absolute cleanliness and Eco-Friendly. Compared with the welding technology of the traditional medical industry, the laser welding machine has obvious advantages in environmental protection and cleaning, and it is unparalleled in terms of process technology. It can realize spot welding, butt welding, stack welding, sealing welding, etc. It has high aspect ratio, small weld width, small heat affected zone, small deformation, fast welding speed, smooth and beautiful weld seam. Don't need for treatment after welding or just need a simple processing. The weld has high quality, no pores, precise control, small focused spot, high positioning accuracy and easy to achieve automation.
Medical device components designed for hermetic and/or structural welds can benefit from laser welding technologies based on size and material thickness. Laser welding is suitable for high temperature sterilization and provides non-porous, sterile surfaces without any post-processing. Laser systems are great for welding all types of metals in the medical device industry and are a great tool for spot welds, seam welds and hermetical seals even in complicated areas.
BEC LASER offers a wide range of Nd:YAG laser welding systems for medical device laser welding. These systems are fast, efficient, portable laser welding systems for high-speed laser welding applications in the Medical Device Industry. Ideal for non-contact welding processes which join two similar or certain dissimilar metals together.
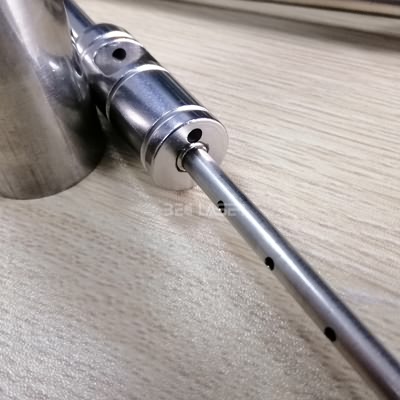
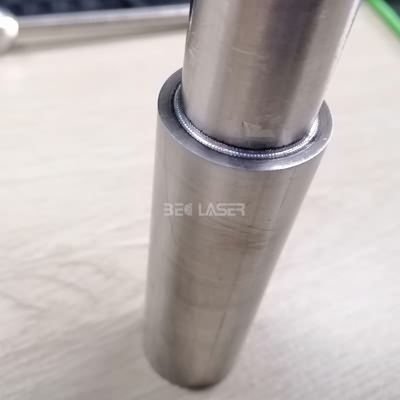
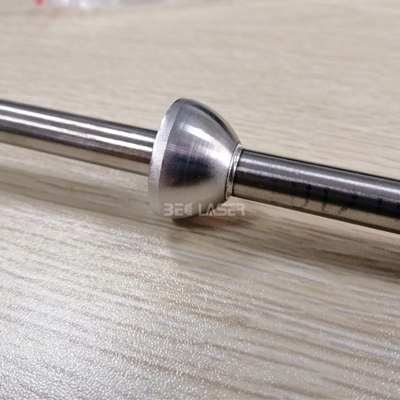